CAROBA® Soft Balancing software
Intuitive and adaptable
The CAROBA® balancing software is the heart of your balancing process. The software manages your workpieces, controls the data acquisition, visualizes the balancing status and provides clear balancing instructions for the selected correction method. The software can be „remote-controlled“ via interfaces to higher-level systems in automated systems - the advantage for you: You work with the same software from laboratory to series production. A variety of additional options adapts your software for special applications, prototype research, process automation or process analysis.
With the CAROBA® balancing software you can balance in a precision range that was previously unattainable.
Your advantages
The CAROBA® Soft Balancing and analysis software
Flexibly expandable, easy-to-use and highly precise.
Our software was specially developed for the requirements of high-precision balancing technology. Specific functions can be optionally programmed for you. If you have any questions about our software package, send us an e-mail or use our contact form.
E-mail : info@pmb-bobertag.de or Phone : +49 631 204015 0
Our Software options
CAROBA® Soft Software options
Outstanding solutions to extend the balancing system for more functions, automation and comfort.
In addition to our standard balancing software, we offer a variety of additional functions that make balancing easier and the daily work with our balancing systems even easier. Modern balancing methods, integration into higher-level control systems, simplified fully automatic operation of your balancing systems, configurable reports at the touch of a button and much more - choose the perfect addition. Special requests or specific functions can be programmed into the balancing software at any time.
We offer standard software options for the following areas:
Balancing methods
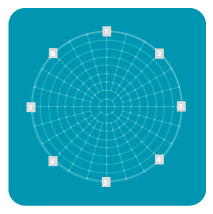
Fixed locations (uniformly distributed)
Specification of the compensation instruction for uniformly distributed fixed locations instead for angles. Simplifies and accelerates the manual balancing process for the operator.
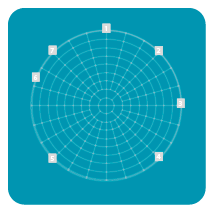
Forbidden zones (fixed locations unequally distributed)
Definition of positions at which no mass compensation may or can be carried out. Thereby defining at which points the unbalance is to be compensated.
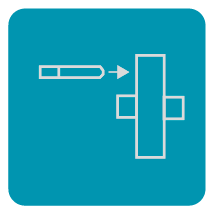
Axial drilling
Correction of unbalance by axial drilling. Output of the required drilling depth with previously defined characteristic values of the drilling tool and the object to be balanced.
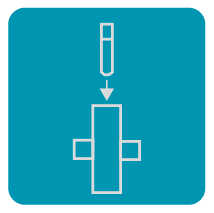
Radial drilling
Correction of unbalance by radial drilling. Output of the required drilling depth with previously defined characteristic values of the drilling tool and the object to be balanced. Consideration of the different consequences at different depths and therefore different effective radius.
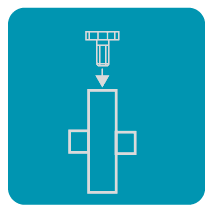
Screws radial
Correction of the unbalance by screwing in or out screws (e.g. grub screws) in threaded holes. The number of rotations required for balancing, in or out, is displayed.
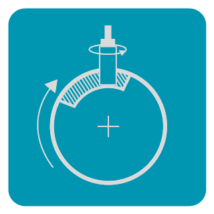
Milling ring segment
The defined milling tool immerses radially into the component. The correction mass is removed as a ring segment.
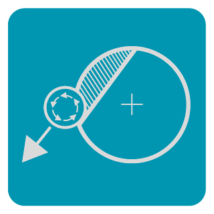
Milling circular segment
The defined milling tool immerses radially into the component and removes the correction mass as a circular segment. A straight edge is created. Only the milling cutter moves.
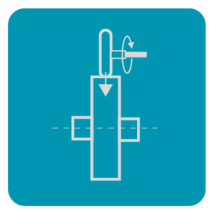
Immerse grinding wheel
The defined grinding wheel immerses radially into the component and removes the correction mass.
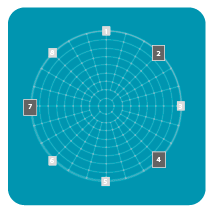
3-mass balancing
An additive correction method, chip-free, easy to use and highly accurate. From a graded stock of balancing weights (e.g. 4 variants) a solution is calculated for a given number of balancing points (e.g. 8 points/circumference), in which 3 of the weights are simultaneously specified at 3 positions in such a way that the result is a highly accurate balancing.
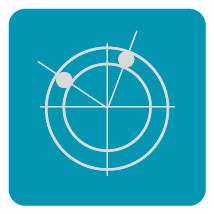
Spread angles
Indication of the angle for the rotation of balancing discs to each other or the adjustment of shifting weights.
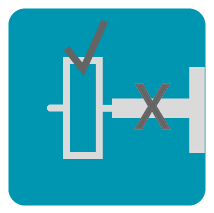
Index balancing
Index balancing mathematically eliminates the influences of the clamping device (e.g. a spindle...) on the workpiece clamped on it. You achieve better balancing results when balancing on spindles.

Magnetic balancing
Balancing is always the elimination of outward acting unbalance forces. When balancing highly magnetic rotating parts, these can be influenced by the earth’s magnetic field. This option calculates this influence and thus enables significantly better balancing results. Even without this option, our balancing systems are “magnet-capable”. However, with this option, you will balance significantly better than your market competitors.
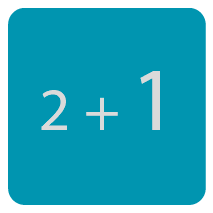
3 plane balancing
The 3 plane balancing provides an additional compensation value for the centre of gravity plane, i.e. the static unbalance. This allows you to improve the static unbalance separately from the dynamic unbalance, whereby some rotor types benefit from better internal forces and torques. You remove the static unbalance in the centre of gravity, which means that less is to be removed in planes 1 and 2.
Comfort features
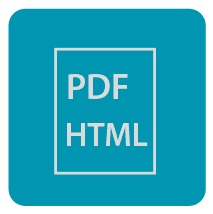
Report generation
Output of a freely configurable report about the balancing process in form of an HTML or PDF file.
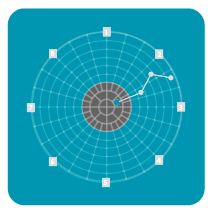
Evaluation criteria
Coloured marking of the required / actual ranges in the polar diagram and the balancing instructions. The operator can see at a glance whether he has already reached the specifications. In automated balancing, this also determines when the automated process transfers the balancing object as good or as reject to the workpiece handling.
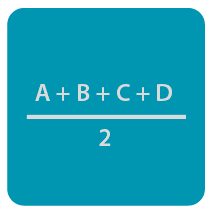
Averaging function
Calculates the average of several measurements. Individual measurements and average values are plotted in the diagrams so that you can see the quality of your setup at a glance. External influences on the result are minimized, limits of reproducible balancing are pushed to better balancing results.
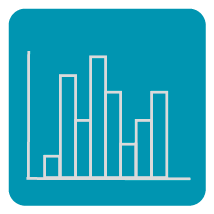
Statistics
Generation and output of statistics with key data such as mean value, scattering and distribution of the unbalance values for series balancing. Freely configurable input data. Very helpful to reveal systematic influences in pre-production and then, for example, to revise injection moulding tools so that less balancing is required.

Cal editing
Helpful for setting up new balancing tasks. You can subsequently change the information given during the identification and thus correct the calibration. For example, you can subsequently shorten runup ramps that were initially set too large and thus saves process time.
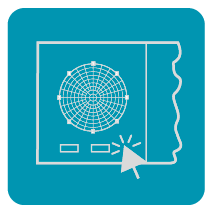
Reduced user interface
User interface reduced for simplified operation. Particularly suitable for manual balancing by semi-skilled assistants. The full user interface can be unlocked by machine setters with a password.
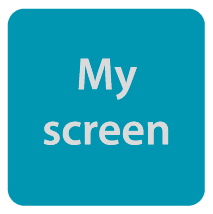
User defined interface
Work surface of the balancing software defined according to your specifications. The full user interface can be unlocked by machine setters with a password.
Ramp-up balancing
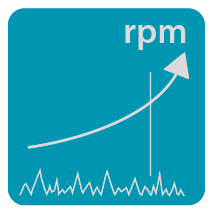
Ramp-up balancing
Instead of measuring at fixed rotational speed, the run-up is recorded and used to calculate the balancing solution. This allows you to change the balancing speed simply by moving a cursor without the need for an additional run. This is a great simplification when setting up new balancing tasks, especially for rotors with difficult to control rotational speed.

Ramp-up balancing 1 sensor for 2 planes
An extension to ramp-up balancing, which is particularly advantageous for high-speed rotors (turbo, dental turbines...). Instead of 2 sensors and one evaluation speed, 1 sensor and 2 evaluation speeds are used. This has advantages for rotors that behave partially elastic at high speeds.
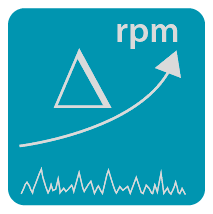
Ramp-up diagrams unbalance + delta
Extension for the ramp-up balancing. Additional diagrams with unbalance over speed and unbalance difference between two balancing operations (delta) over speed are displayed. Helpful for selecting the optimal balancing speed when setting up new balancing tasks.
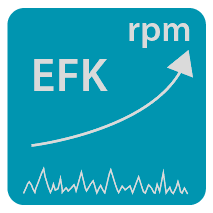
Ramp-up diagrams transfer function + IC + process characteristics
These additional options for the ramp-up method support process developers for new balancing tasks and series balancing. If you would like more detailed information, please do not hesitate to contact us.
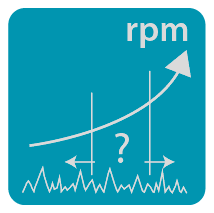
Analysis assistant
In the ramp-up balancing, analysis speeds are selected manually by the setter or operator. The analysis assistant automates this for tasks with challenging rotor behaviour. After a few test measurements, a preset of good settings is automatically generated.
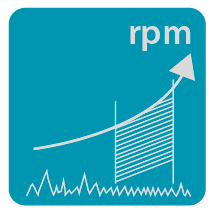
Optimized ramp-up balancing
An extension of the ramp-up balancing. This method calculates solutions that are characterized by a minimum area under the acceleration curve. This special procedure is particularly used for series balancing in the production of turbochargers.
Extended evaluation
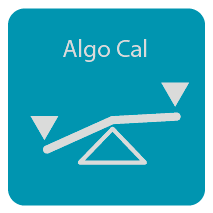
Auto-learning algorithm
The software learns to automatically adjust the phase and magnitude of removal, even with gradually changing pre-production. This compensates for tool wear and reduces the number of removals per workpiece. Improves the cycle time.
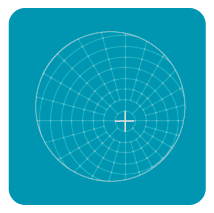
0-point offset
To balance to a specific unbalance (offset), you can specify it here. E.g. manual compensation of the unbalance of a balancing adapter. E.g. targeted unbalance of a component which is compensated by another targeted unbalance after assembly by other components.
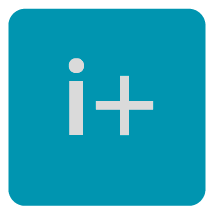
Advanced Calculations
Extended information on characteristic values, the identification and the distribution of the unbalance over the bearings of the balancing object. Very well suited for simulating the effects of changes in the design of rotating parts (e.g. bearing distance) on the unbalance situation („What if...“).
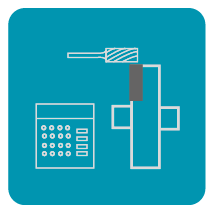
Material removal calculator
For automated balancing systems, calculates the removal profile for unbalance correction with grinding or milling tools. Incl. internal logging (where mass already has been removed, it cannot be removed again in the following step).
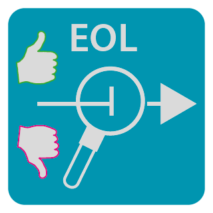
EOL (End of line test)
Often an assembly is rotating in the balancing machine for the first time. With the EOL option, this assembly is now evaluated according to further criteria in addition to the balancing, independent of the balancing result. Thus, despite good balancing, workpieces with, for example, conspicuous (defective or incorrectly installed) bearings can be detected. It is an early end-of-line test to avoid unnecessary further assembly costs by sorting out these workpieces.
Interface and automation
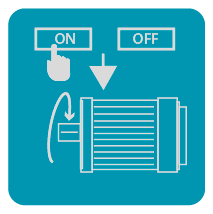
Drive control
Control of drives by UMS (hardware, unbalance measuring system). Controls the drives of our complete systems as well as your own drives. Output of set values for DC motors, frequency inverters (VFD), air drives and CAN bus commands. Manual operation possible, automated remote control by the balancing software is the most used standard.
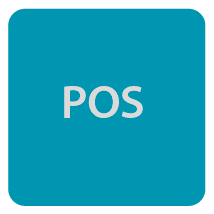
POS
Module for controlling stepper motors for positioning the balancing objects for mass removal. For automated mass correction in machines or manual marking of the removal position by the operator.
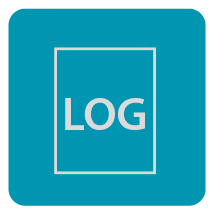
Logging
Creates a log file with one line for each individual balancing object. This line contains all relevant balancing values. Machine and human readable.

TCP-API
Module for remote control of the balancing software via customer control programs. The connection is made via TCP protocol. Excellent solution for integration into superior automation controls.

SAP web service
Characteristics of the balancing object are transferred directly from/to an SAP system installed at the customer’s site. Serial numbers are checked for plausibility, incorrect workpieces are reported to the operator. Balancing recipes (rotor file, calibration) are loaded according to the serial number. Our interface to Industry 4.0

User interface “Status”
Reduced status screen as user interface particularly suitable for automated operation. It is not possible for the operator to exert any influence. The full user interface can be activated by the setter with a password.